Sayama – the right fit when it needs to fit right
Sayama’s expertise is not limited to medical devices, but extends to semiconductors, optics, electronic components, and a wide range of other cutting-edge precision microtechnologies.
This broad application base enables us to solve our clients’ technical issues, reduce overall costs, and shorten lead times thanks to technical capabilities that others specializing only in medical devices may lack.
-
Lead time
For the best “Go”, you need the best “Ready, set”
Sayama can produce faster than elsewhere because we design with product specification and our accumulated know-how necessary for mold design and manufacturing to avoid defects. Since mold optimization is conceptualized at the same time product designs are modeled, the lead time is overwhelmingly shorter than the process by which other producers may modify the product or incorporate additional processing steps after manufacture. Faster overall manufacturing means not missing out on sales opportunities.
-
Incomparable quality
Our expertise opens your possibilities
We continue to be part of the world’s most-advanced technological developments in cutting-edge, precision microtechnologies. Sayama works in a wide variety of resins and metals, which means we can make optimal proposals to our clients. This ensures the same, highest level of quality from prototyping through to mass production, which in turn eliminates as many quality-control issues as possible. With this level of entrustment from clients and our track record of results and innovations, Sayama can realize products that pose technical challenges for others.
-
Cost certainty
Delivered right the first time
The greatest cost for clients is when rework is required – whether design revision or additional processing steps after casting. Sayama plans projects closely with clients, considering the best overall processes from the pre-production stage. This makes Sayama unique, in that we do not simply sell components at set prices, but we provide production suggestions and proposal revisions to contribute to the optimal total cost for clients.
-
Total coordination
Stream-lined execution
In order to bring whole-package solutions to clients beyond plastic-molding dies and molds, we can also procure other components related to the product in question and the associated technical support. This allows clients to rationalize procurement processes and achieve improved QCD performance.
Showcase
Our clients present us with challenges for smaller components for thinner devices and applications for less-invasive surgical equipment and medical devices. Thanks to this, we have capabilities that aren’t widely known today, which will lead to the possibilities for tomorrow. Here is only a small selection of some recent projects. For your particular application, reach us via the Contact Form with an outline of what you’d like to discuss.
-
Medical analysis
Microfludics Molding
Injection molding / PC (Polycarbonate)
Channel dimensions: Depth 0.1mm – Width 0.1mm
Design integrated with lure ports
-
Innovation
PEEK resin hypodermic needle
Injection molding / PEEK
Needle size: Outer Ø 0.24mm – Inner Ø 0.07mm
Thinnest wall: 0.085mm
-
Medical
Micro Molding with PEEK and MIM
Babcock forceps
Injection molding / PEEK
Metal Injection Molding(MIM) / SUS
-
Medical
Maryland’s dissector
Metal Injection Molding(MIM) / SUS
-
Medical analysis
Microchannel
Injection molding / COP (Cyclo Olefin Polymer)
Channel dimensions: Depth 0.15mm – Width 0.1mm
-
Innovation
Micro Dispencer Nozzle
Metal Injection Molding(MIM) / SUS
Hole diameter: 30μm
-
Innovation
Combination of insulator, micro fluidics and test socket
Injection molding / PC(Polycarbonate)
286holes / φ0.60mm - 0.80mm pitch
Channels / 0.03mm wide - 0.03mm deep
Ribs / 0.15mm thick - 0.4mm pitch
-
Innovation
0.08mm Pitch Connector
Injection Molding / LCP (Liquid Crystal Polymer)
Size: Width 0.8 mm - Height 2.5 mm - Depth 0.5 mm
Weight: 0.0025g
-
Innovation
Planetary Gear
Injection molding / POM(
Polyacetal)
Diameter: Outer 0.5mm - Inner 0.25mm
Module: 0.025
-
Innovation
Waterproof connectors
2k injection molding
Liquid injection molding
PBT(polybutylene terephthalate)
LSR(Liquid Silicone Rubber)
Your partner
before,
during and after
production
Realize more than you might imagine possible by utilizing our experience and continually evolving expertise accrued over the course of 60 years and over 2,300 dies and molds. We can assist in the R&D and prototyping stages by advising on materials and manufacturing possibilities to meet the demands of ever-miniaturizing applications, through to market roll-out, and then beyond as you plan the next iteration of your product or entirely new products. We always aim to deliver at a level that makes Sayama a partner that is indispensable.
Plastics & metals
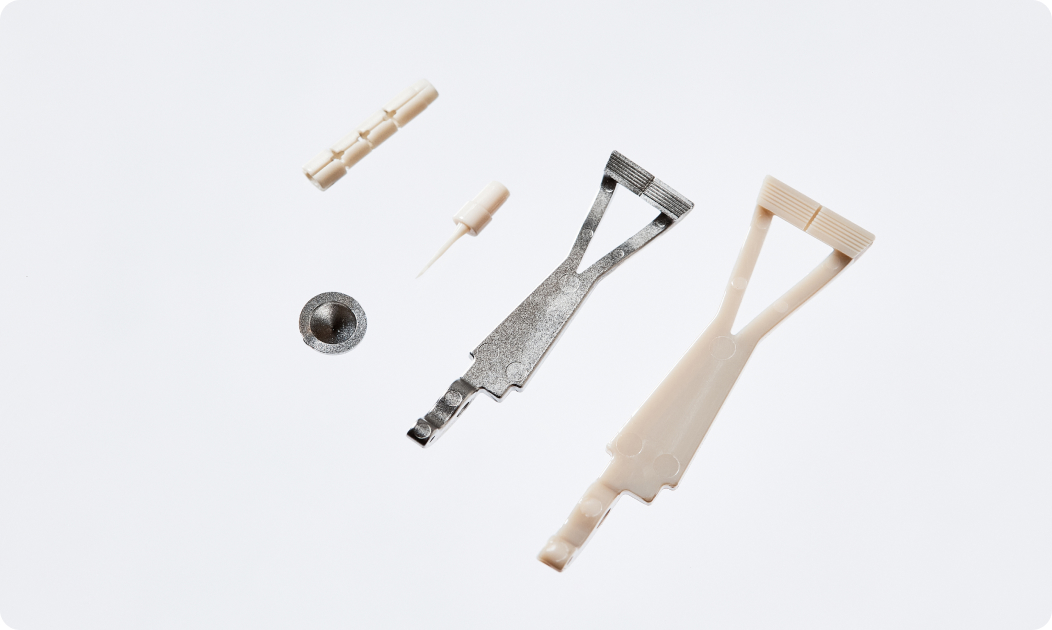
Plastics & metals
Many molding manufacturers produce in metal or plastic only. Sayama does both. The obvious benefits for clients are time and cost thanks to the ability to work with a single production partner that has knowledge of how components will integrate and how to optimize processes and production to achieve cost efficiencies.
Resins we have experience producing in include: PEEK / COP / PEI / PES / LCP / PPS / POM / PP / PA / PBT / PMMA / PAI / EP / PF/ MIM (Ti, SUS, Cu)
Innovation
As a leader in micro molding, we have been fortunate to work with other world leaders in pioneering new devices and technologies. This tests us to keep innovating with materials and techniques to achieve even greater miniaturization. Not only that, but by pushing the limits of our tools of production we have been able to achieve accuracies in our finishing that exceed the outcomes rated by manufacturers. Our track record in innovation comes from achieving the desired outcomes where others have faced challenges.
Philosophy & future
The results and levels of precision we
achieve are the blend
of people, environment and technology.
-
People
The Sayama family grows slowly, and stays together. They bring their minds and skills, and we provide an atmosphere that enriches through challenges and the satisfaction of arriving at solutions together. While the company has its ambitions, it is our responsibility to help our employees realize their dreams, too. The clients we work with also contribute to our successes by entrusting us to be part of their projects that may save or protect lives, or enrich the quality of lives through their vision of what the future could hold.
-
Environment
Literally nestled in the foothills before the mountains of Saitama, part of our production facilities are located belowground to assist with temperature control in order to minimize deformations in molds. External vibration is extremely low thanks to being located away from roadways that carry heavy traffic. Looking out the windows to the neighboring tea fields and our door handles in the common areas that have been repurposed from prunings of the sakura tree by the roadside infuses the Sayama facility with nature.
-
Technology
Investing in upgrades or additions to the tool fleet is about recognizing and rationalizing when the need fill a gap or usefulness brought about by advancements is now “right” for Sayama. New technology leads to the development of new techniques, which leads to new processing capabilities through experimentation and discovery. At the same time, it’s satisfying when not-as-new technology continues to demonstrate its usefulness in the hands of master operators and craftspeople.
The nature of the work we do means that we have one foot in the future, and it’s with that mindset that you will find a handwritten statement of intent on the wall of our [which room] that is our Environmental Philosophy that informs how we go about what we do. Translated, it reads:
Sayama Mold Manufacturing Co., Ltd. is strongly aware that as a manufacturer of molds and engineer of plastic-related products, our business activities are closely related to the global environment.
In carrying out our business activities, we not only comply with laws and regulations, but
also consider environmental issues in order to pass on the current global environment to the children of the next generation, and each employee actively works to protect the
environment and makes continuous improvements, creating a safe and hygienic workplace and fulfilling our corporate social responsibility.
Meet Soichiro Oba – CEO
Sayama Mold Manufacturing Co., Ltd.
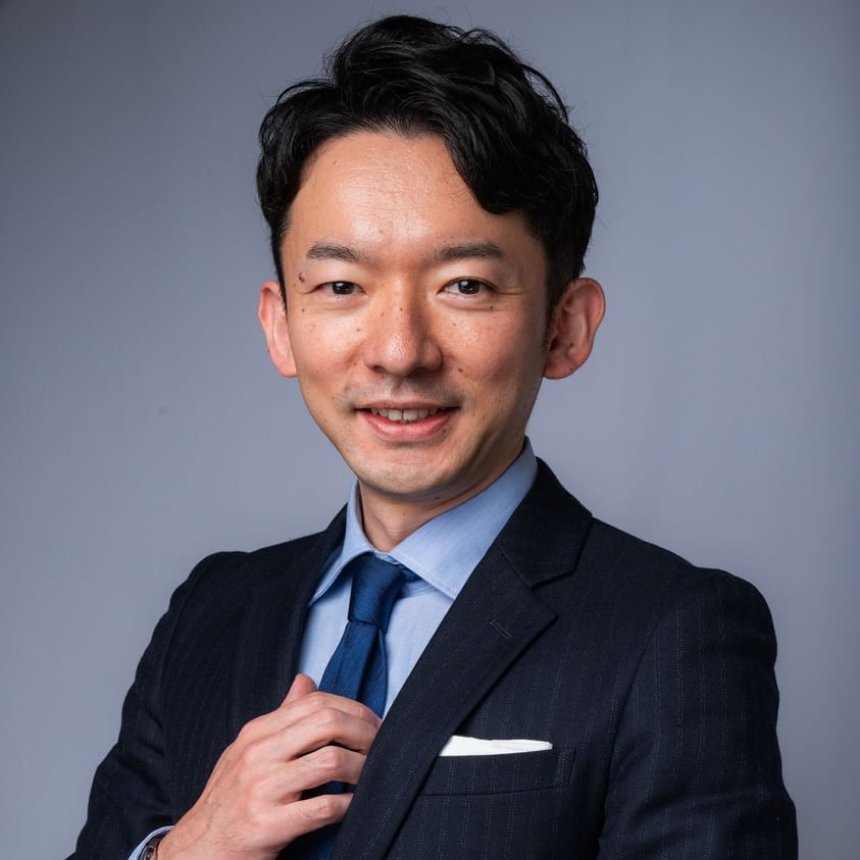
Sayama’s appeal – especially in the field of micro-precision machining and finishing – is our unrivaled technology and having been involved in the foundation of global innovation in various fields.
We’re here to support startups in the medical field realize their innovative ideas to broaden life-saving and life-enriching technologies and devices.
Similarly, we have enabled and continue to enable established medical device manufacturers commercialize their products to treat, assist, and rehabilitate patients across the globe. This is thanks to the combination of our technology and expertise, but also importantly Sayama’s belief in the value in saving and maintaining people’s lives.
The desire for our clients to succeed in their fields to bring happiness to others has helped define our mission and to value the critical part we play in helping them achieve their successes. Even the tiniest components are able to have a massive impact.
The reason we have been in this business for 60-plus years is due to our strong desire to take challenges presented to us from “might be able to” to “are able to”.
Counting down to our 100th anniversary …
Contact
Contact us to discuss your project with one of our micro molding experts.